Safe work practices have been the foundation of what is expected in mining, construction, farming, and manufacturing. In Australia we have many workers in remote locations and at risk sites which is why it is a legal and moral duty to prevent harm and improve safety. At first we had very basic safety measures which included things like written check lists, physical inspection of equipment, and spot checks by supervisors. Those early measures did provide some protection but for the most part they were reactive to issues which also had the issue of people missing things or delays in reporting.
Now, smart tools have started to change how everyone handles worker safety at a deep level. Adding digital options like Internet of Things (IoT) and artificial intelligence (AI) brings real-time, data-heavy safety choices at job sites. For example, a man down alarm relies on position and movement sensors to spot if a worker drops or cannot move, quickly telling bosses or emergency helpers. This instant warning helps most in alone work areas, like mines below ground or remote farms in Australia, because fast rescue is hard.
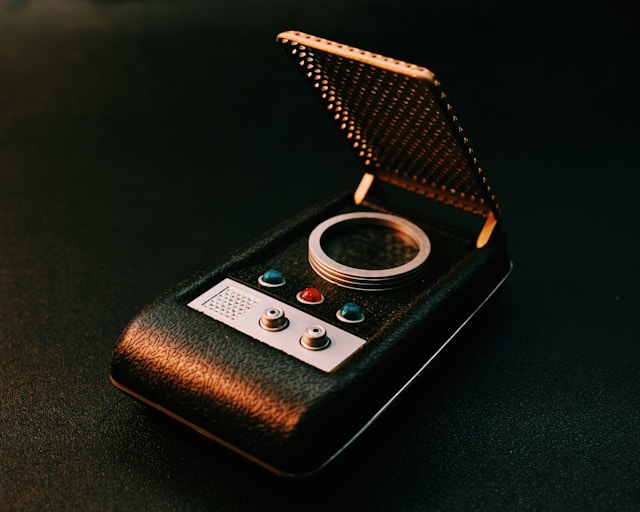
From Paper Logs to Digital Monitoring
Old safety changes first worked by making rules and writing down checks by hand. Teams used daily lists, check forms, and papers for accident notes, all put together without computers. Over years, digital software replaced some books and made collecting details quicker and mistakes lower, but these tools still reported events after they happened. If someone missed a risk during a check or forgot to officially log a problem, the threat stayed hidden. Computer screens and data tools saved time, but they lacked speed for instant injury prevention. As IoT arrived, safety teams got systems that linked tools, people, and their work areas. Sensor tech could measure and send reports about room heat, machine health, or how people moved while on shift. A temperature sensor might show dangerous heating in a machine, and vibration trackers might find a weak pipe before it broke for real. Instant warnings gave site leaders a chance to fix problems before real trouble started.
Wearable Tech and Smart PPE
Wearable safety gadgets improved worker support a great deal in the last few years. These devices, placed into uniforms or personal protective equipment (PPE), watch both body signs and work conditions. A smart helmet might check if someone’s head moves too much or if the person becomes slow at work, and a smart vest could feel changes in heart level or spot gas in the air. When people work in desert sites or drill oil at sea, help could take a long time to reach the area, so tools like these often keep people alive. Devices track how the team’s health changes and flag odd danger signs so help reaches faster. Info taken over many weeks can be reviewed to see big work patterns, and then bosses may change plans or move work time to lower the chance of tiredness or harm.
AI-Powered Risk Prediction and Automation
Artificial intelligence brings new risk control into industry by using prediction abilities. By checking big data from sensors, old work reports, and weather information, AI spots risks before harm happens. Machine learning systems calculate when machines might break and set a warning for fixing things early so injury does not occur. Automated checks are possible now because AI runs drones and robots with cameras and sensors. They look at high places, tight rooms, or places with chemical problems, keeping workers away from risk. The devices notice faults, metal damage, or leaking faster than people’s eyes, then send repair news to teams with no wait. In fields like mining or energy, where working areas change and are hard, this smart checking helps a lot for safety and work speed.
Connectivity and the Future of Emergency Response
Safety systems today use strong digital links and connected tools. Cloud-based networks join data from wearables, sensors on posts, and drones in one dashboard with up-to-second updates. Emergency plans move with these changes. When a worker falls in a far corner of a mine, the safety suit or helmet gives position and health data right away to the main office. Special features like geo-fencing or location tracking tell rescue teams the exact place to go and main things they need. For Australia, where job sites spread over wide empty land, the fast answer from these tools changes emergency care. Response times go down, serious injuries get lower, and more people get help in time. As the tech drops in cost and firms connect the systems more, even smaller rural jobs can try these new safety ways, not only large city companies.
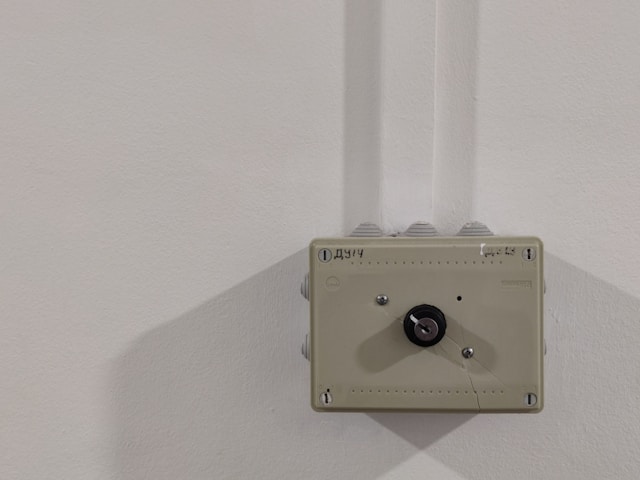
The Evolution from Manual Protocols to Smart Sensors
The shift from traditional paper reports to digital sensors is a large step in safety. We went from log books and sometimes manual inspection to constant sensor update, future risk models, and automatic safety measures which out go the old ways. In Australia which has large distances and tough weather we are seeing these changes become the norm not the exception in what we do to protect all workers.